一、浸焊(Immersion Soldering)
PCBA加工浸焊工藝為最早出現(xiàn)的簡單做法,系針對焊點較簡單的大批量焊接法(Mass Soldering),目前一些小工廠或實驗做法仍在使用。系將安插完畢的板子,水平裝在框架中直接接觸熔融錫面,而達到全面同時焊妥的做法。其助焊劑涂布、預熱、浸焊與清潔等連續(xù)流程,可采手動或自動輸送化,則端視情況而定,但多半是針對PTH插孔焊接而實施浸焊。SMD之貼裝零件則應先行點膠固定才可實施,錫膏定位者則有脫落的麻煩。
二、波峰焊(Wave Soldering)
PCBA加工波峰焊工藝是利用已熔融之液錫在馬達幫輔驅動之下,向上揚起的單波或雙波,對斜向上升輸送而來的板子,從下向上壓迫使液錫進孔,或對點膠定位SMD元件的空腳處,進行填錫形成焊點,稱為“波峰焊”。此種“量焊”做法已行之有年,即使目前之插裝與貼裝混合的板子仍然可用?,F(xiàn)將其重點整理如下:
1、助焊劑
波峰焊連線中其液態(tài)助焊劑在板面涂布之施工,約有泡抹型、波浸型與噴灑型等三種方式,即:
1.1 泡抹型Flux:
系將“低壓空氣壓縮機”所吹出的空氣,經過一種多孔性的天然石塊或塑膠製品與特殊濾心等(孔徑約50~60µm),使形成眾多細碎的氣泡,再吹入助焊劑儲池中,即可向上揚涌出許多助焊劑泡抹。當PCBA組裝板通過上方裂口時,于是板子底面即能得到均勻的薄層涂布。并在其離開前還須將多余的液滴,再以冷空氣約50~60℃之斜向予以強力吹掉,以防對后續(xù)的預熱與焊接帶來煩惱。并可迫使助焊劑向上涌出各PTH的孔頂與孔環(huán),完成清潔動作。至于助焊劑本身則應經常檢測其比重,并以自動添加方式補充溶劑中揮發(fā)成份的變化。
1.2 噴灑型Spray Fluxing:
常用于免洗低固形物(Low Solid;固含量約1-3%)之助焊劑,對早先松香(Rosin)型固形物較高的助焊劑則并不適宜。由于較常出現(xiàn)堵塞情形,其協(xié)助噴出之氣體宜采氮氣,既可防火又能減低助焊劑遭到氧化的煩惱。其噴射的原理也有數(shù)種不同的做法,如采不鏽鋼之網狀滾筒(Rotating Drum)自液中帶起液膜,再自筒內向上吹出氮氣而成霧狀,續(xù)以氮氣向上吹出等方式進行涂布。
1.3 波峰型Wave Flux:
直接用幫輔及噴口向上揚起液體,于狹縫控制下,可得到一種長條形的波峰,當PCBA組裝板底部通過時即可進行涂布。此法可能呈現(xiàn)液量過多的情形,其后續(xù)氣刀(Air Knife)的吹刮動作則應更為徹底才行。此種機型之價格較泡抹型稍貴,但卻比噴灑型便宜,其中溶劑的揮發(fā)量也低于泡抹型。
2、預熱
一般波峰焊前的預熱若令朝上板面昇溫到65~121℃之間即可,其昇溫速率約2℃/S~40℃/S之間。預熱不足時助焊劑之活性發(fā)揮可能未達極致,則焊錫性很難達到最佳地步。且在揮發(fā)份尚未趕光之下,其待焊表面的助焊劑黏度仍低時,將導致焊點的縮錫(Dewetting)與錫尖(Solder Icicles)等缺失。但預熱溫度太高時,則又可能會對固形物太低的免洗助焊劑不利,此點須與助焊劑供應商深入瞭解。
3、波峰焊工藝管控
3.1 錫溫管理:
目前錫池中焊料的合金成份仍以Sn 63/Pb37與Sn 60/Pb40者居多,故其作業(yè)溫度控制以260º±5℃為宜。但仍須考量到待焊板與零件之總體重量如何。大型者尚可升溫到280℃,小型板或對熱量太敏感的產品,則可稍降到230℃,均為權宜的做法。且還須與輸送速度及預熱進行搭配,較理想的做法是針對輸送速度加以變換,而對錫溫則以不變?yōu)橐耍蝈a溫會影響到融錫的流動性(Fluidity),進而會衝擊到焊點的品質。且焊溫升高時,銅的溶入速率也會跟著增快,非常不利于整體焊接的品質管理。
3.2 波面接觸:
自PCBA組裝板之底面行進接觸到上涌的錫波起,到完全通過脫離融錫涌出面的接觸為止,其相互密貼的時程須控制在3-6秒之間。此種接焊時間的長短,取決于輸送速度(Conveyor Speed)及波形與浸深等三者所組成的“接觸長度”;時程太短焊錫性將未完全發(fā)揮,時程太長則會對板材或敏感零件造成傷害。若該波峰焊連線是直接安裝在一般空氣中時,則錫波表面會不斷形成薄薄的氧化物,由于流動的原因與PCBA組裝板(PWA)不斷浮刮帶走,故整體尚不致累積太多的氧化物。但若將全系統(tǒng)尤其是波峰焊段采用氮氣環(huán)境所籠罩時,則可大大減少氧化反應的發(fā)生,當然也就使得焊錫性有了顯著的改進。
輸送PCBA組裝板的傳動面須呈現(xiàn)4º~12º的仰角,如此將使得零件本體的后方,被阻擋之“背風波”錫流不強處的焊接動作大獲改善。一般現(xiàn)行波峰焊機均設有可單獨控制的雙幫輔與雙波(錫池則單雙波均有),前波呈多股噴泉式強力上涌者稱為“擾流波(Turbulent Wave)”,系逼迫強力錫流穿過多排各種直徑的迂迴小孔而形成,可直接衝打到行走中的底板表面,對通孔插腳或貼裝尾部接腳等焊接非常有利。之后遭遇到的第二波,則為呈拋物線狀的“平滑(流)波(Laminar Wave)”對朝下板面的接觸時程較長,就板面需填錫補錫的引腳有利,且還可消除過多的錫尖。某些商品機種還可另行加裝熱空氣(或熱氮氣)的刮錫設施于第二波之后,也可消除錫尖與焊點的過多錫量。
對于板面眾多的小型片狀零件(如Chip Resistor或Chip Capacitor)而言,〝擾流波〞附帶的機械打擊力量,還可迫使錫流包圍零件四周甚至進入腹底,使其等所形成的焊點更為完整,任何局部的缺失還可被隨即報到的〝平流波〞所再補足。且此第二波中亦可加裝額外的振動裝置,以增加波流對板面所施展的機械壓力。
3.3 接觸的細節(jié):
若再仔細深入探討其瞬間接觸焊接的細節(jié)時,還可再分述于后:
(1)板面與擾流波接觸的初期,助焊劑立即進行揮發(fā)與分散的動作,連帶使得待焊的金屬表面也開始沾錫(Wetting)。此波中也可再加裝低頻的振盪裝置,以加強與配合其待焊面接受助焊劑的搓擦動作。如此將可對貼裝零件腳之填錫補錫大有助益,并可減少背風坡處的“漏焊”(Skipping)現(xiàn)象。當然在雙波的先強勁與后溫柔的不同作用下,整體焊錫性也將會更好。
(2)當板面進入錫波中心處的“傳熱區(qū)”(Heat Transfer Region)時,在大量熱能的推動下,Wetting瞬間的散錫(Spreading)動作也迅速展開。
(3)之后是錫波出口的“脫離區(qū)”(Break Away),此時各種焊點(Solder Joint)已經形成,而各種不良缺點也陸續(xù)出現(xiàn)。PCBA組裝板若能快速順利的脫離錫波則萬事太平。難捨難分的拖錫,當然就會成為不良錫橋(Solder Bridge)或錫尖(Solder icicles)甚至錫球(Solder Ball)的主要原因。其脫離的快慢雖直接取決于輸送速度,但刻意將輸送帶平面上仰4º~12º時,還可借助重力的協(xié)同而能更乾脆而方便的分開。至于該等拖泥帶水造成的板面缺點,當然還有機會被隨后即到的熱風再加修整。此時卻不能用冷風,以免造成組裝品溫度過度起伏的熱震盪(Thermal Shock)不良效應。
3.4氮氣環(huán)境的協(xié)力:
在免洗助焊劑的弱勢活力下(只含Carboxylic Acid羰酸1%而已),還要奢求更好的焊錫性,豈非緣木求魚搟面杖吹火?然而迴避溶劑清洗之環(huán)保壓力既不可違,當然只好另謀他途尋求解決。于是當波峰焊線之錫池區(qū),若能改裝成氮氣環(huán)境以減少氧化的不良反應者,自然大大有助于焊接。經過眾多前人試驗的結果,氮氣環(huán)境的錫池區(qū)其殘氧量以100ppm以下的焊錫性最為良好,然而其成本的額外增加自是不在話下。為了節(jié)省開支,一般實用規(guī)格多半都將殘氧率范圍訂定在500ppm至1000ppm左右。也曾有人將甲酸的氣體引入氮氣環(huán)境中,或加用在助焊劑中,以其強烈的還原性協(xié)助減少氧化反應的發(fā)生。然而此種具毒性的刺激物質,其在室內的揮發(fā)濃度卻不可超過5ppm,以免對人體造成傷害。設計良好的“氮氣爐”其待焊件的進出口與充氣裝置等動態(tài)部份,都已做好隔絕密封的設施,自可減少氮氣的無謂消耗,此等氮氣爐波峰焊線具有下列效益:
(1)提升焊接之良率(yield)。
(2)減少助焊劑的用量。
(3)改善焊點的外觀及焊點形狀。
(4)降低助焊劑殘渣的附著性,使之較易清除。
(5)減少機組維修的機率,增加產出效益。
(6)大量減少錫池表面浮渣(Dross)的發(fā)生,節(jié)省焊錫用量,降低處理成本。
深圳宏力捷推薦服務:PCB設計打樣 | PCB抄板打樣 | PCB打樣&批量生產 | PCBA代工代料
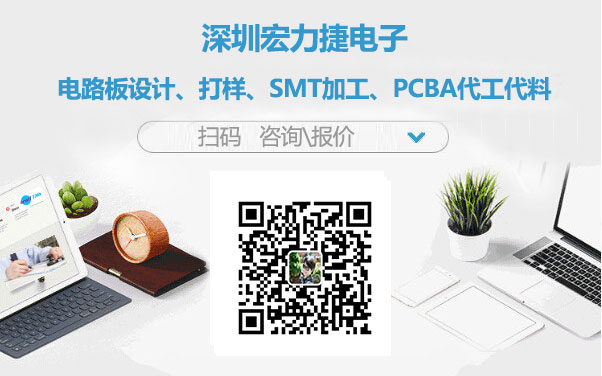